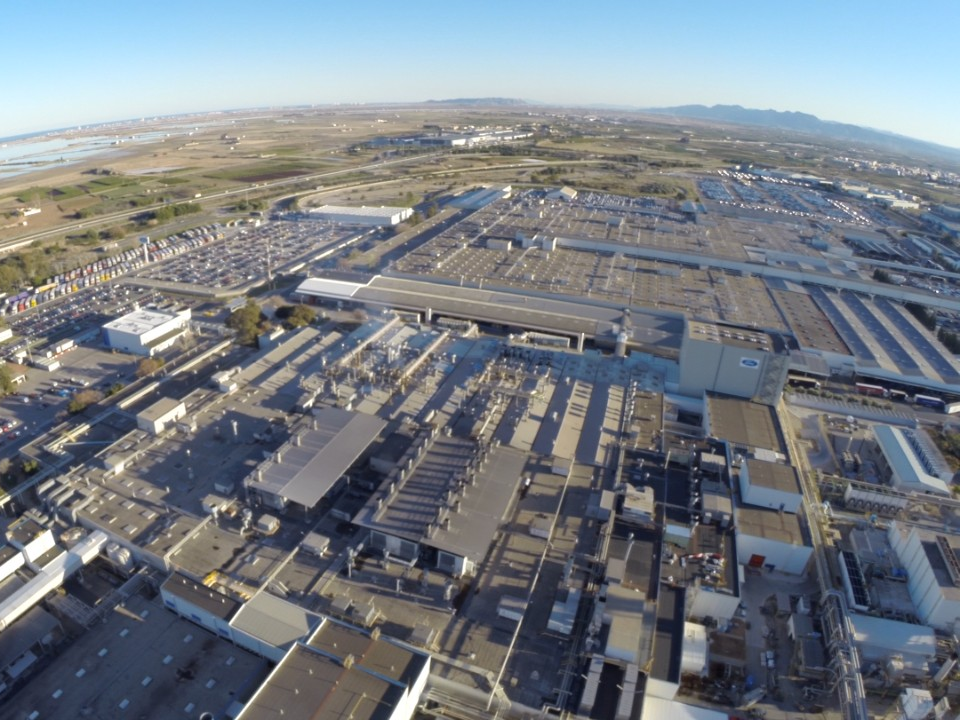
- Ford Motor Company invests $2.6 billion since 2011 in Valencia, Spain, manufacturing operation; largest ever investment in Spain’s auto industry
- Vehicle production in Valencia will increase 40 per cent to around 400,000 units in 2015; new high-tech bodyshop raises daily production capacity to 2,000 vehicles
- With six nameplates in 2015, even more bodystyles, and the capacity
to manufacture up to 450,000 vehicles a year, Valencia is one of Ford’s
largest and most flexible plants worldwide
- Ford Valencia operations now employ 8,000 people, up from just below 5,000 in early 2013; supplier operations supporting Valencia production have increased employment by 1,500 jobs since 2013
- Valencia plant currently builds Mondeo wagon, five-door, and four-door including Mondeo Hybrid, Kuga SUV, Transit Connect light commercial vehicle and Tourneo Connect people-mover; all-new S-MAX multi-activity vehicle, Galaxy seven-seat people-mover and Vignale Mondeo go into production later this year
- Valencia is one of Spain’s top automotive exporters, with 80 per cent of its production to 75 countries worldwide, including North America
VALENCIA, Spain, Feb. 5, 2015 – Ford Motor Company today announced it is completing the final part of a $2.6 billion investment in its Valencia, Spain, manufacturing operations, transforming it into one of the world’s most advanced, flexible and productive auto plants.
The investment by Ford is the largest in the history of Spanish auto industry and will allow the Valencia plant to increase vehicle production by 40 per cent this year to about 400,000 vehicles, and will have the capacity to potentially build up to 450,000 vehicles a year.
Valencia also is today one of Spain’s top automotive exporters, with 80 per cent of its production being exported worldwide.
Ford now employs about 8,000 people at the facility, up from just below 5,000 in early 2013. Supplier operations supporting Valencia production also have added 1,500 jobs since 2013.
“This world-class facility will help Ford’s accelerate its growth in Europe and around the world,” said Mark Fields, Ford president and chief executive officer. “Valencia is not only a major hub of production – building vehicles and engines exported to 75 countries worldwide – but also a centre of innovation employing some of the industry’s most advanced lean, flexible and environmentally friendly manufacturing processes.”
In 2015, Valencia will build six Ford nameplates and even more body styles. The plant currently builds the all-new Mondeo wagon, five-door, and four-door including the Mondeo Hybrid, Kuga SUV, Transit Connect light commercial vehicle and Tourneo Connect people-mover. The all-new S-MAX multi-activity vehicle, Galaxy seven-seat people-mover and the Vignale Mondeo go into production later this year.
The investment consisted of an initial $1.25 billion announced in 2011, followed by a further $1.37 billion since 2013. Valencia will be the sole European production source for all six Ford nameplates assembled at the plant.
Flexible, modern and efficient
The Ford Valencia facility has produced more than 11 million vehicles and 15 million engines since production started in 1976. The plant was officially opened by King Juan Carlos and Henry Ford II helping Spain emerge from decades of isolation from the global economic stage.
Almost 40 years later, the plant is at the forefront of Ford’s plan to accelerate the pace of the progress on its One Ford plan, deliver product excellence and incorporate innovation into every part of the business.
A new 89,000 m2 bodyshop constructed over nearly eight months raises the plant’s vehicle production capability to about 2,000 units per day. For production of Mondeo and Mondeo Hybrid, the plant was retooled to deliver an industry-first application of hydro-formed high strength steel.
Ford has constructed an additional paint shop, installing automated paint processes that remove the need for paint-drying between application stages, and dirt detection technology. This improves quality while delivering energy and productivity savings.
New assembly line processes make Valencia among Ford’s most efficient facilities, essential to managing the increased complexity of producing more models and derivatives than any Ford facility in Europe. For example, in line with the global Ford Production System, all production components are now transported alongside the vehicle in a pre-assembled kit, saving time and effort.
Since 2011 more than 900 new robots have been installed in the Valencia bodyshops, and 34 in the final assembly areas to help deliver the highest quality standards. Nearly 600 highly skilled engineers are involved in supporting the high-tech production processes in Valencia.
“Mondeo, S-MAX and Galaxy will grow the number of parts we manage from 7,000 to 18,000, requiring some fresh and innovative solutions,” said Tony Ades, operations manager, Valencia. “Strong relationships with unions and local government have been essential to developing a flexible facility that can respond quickly and efficiently to changes in demand for our vehicles, with a highly trained and motivated workforce able to operate across our assembly lines.”
Last year, the plant contributed to Ford’s sustainability goals by recycling 3,850 tonnes of wood, paper and cardboard, and by improving its efficiency in water and electricity consumption per car by three per cent.
Vignale Center
Valencia will in 2015 also complete a new Vignale Center, a specially-created department dedicated to ensuring exacting levels of quality and fulfilling customer expectations of Ford’s new upscale Vignale product and ownership experience.
Vignale debuts this year with the Ford Vignale Mondeo, and each vehicle will pass through an additional sign-off process where trained experts will assess criteria including paint finish and panel alignment assisted by the latest laser and camera technology.
“Ford is the engine behind automotive industry growth in Spain,” said Jose Machado, chairman, Ford of Spain. “The combination of innovative product, forward-looking investment, strong local relationships, and hardworking, flexible employees will continue to deliver meaningful progress in improving our overall business in Europe.”
